Рубрика: Заводы и производства
Компания Клингер: опыт производства арматуры для атомных станций
О.Писарева, руководитель бюро ООО «Клингер Флуид Контрол Гмбх», Санкт-Петербург
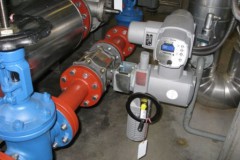
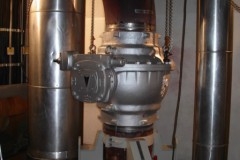
- конструктивные особенности запорной арматуры Клингер, сочетание ремонтопригодности без демонтажа из трубопровода и легкости ремонта с
отсутствием необходимости в обслуживании; система двойной герметичности шаровых кранов Баллостар®, исключающая пропуск рабочей среды даже при выходе из строя одного уплотнительного элемента, подтвержденное сохранение герметичности класса «А» после значительного количества циклов (до 120 тысяч в зависимости от номинального диаметра, испытание на большее количество циклов возможно по конкретным техническим условиям заказчика). Об этих конструктивных особенностях мы уже неоднократно подробно писали, в том числе и на страницах журнала «ТПА»,
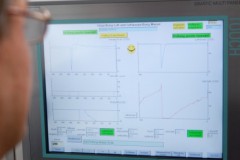
- наличие уникальной технической базы, самых современных испытательных стендов и аккредитованной TÜV Австрия испытательной лаборатории.
Компания Клингер Флуид Контрол на производственной площадке в г. Гумпольдскирхен располагает тремя испытательными подразделениями: лаборатория конструкторского бюро, где проводятся испытания опытных образцов, моделей, проводится наработка на отказ, другие испытания, связанные и изменением конструкций существующих линеек и разработкой новой продукции; испытательные стенды в конце производственного цикла для приемки готовых изделий; оборудованная испытательная лаборатория отдела контроля качества,
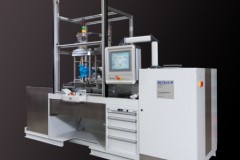
- длительный опыт сотрудничества с компанией Аума, имеющей отличные референции и опыт изготовления электроприводов для атомных станций, как в общепромышленном, так и в специальном исполнении,
В Западной Европе для поставок на АЭС не предполагается централизованного лицензирования, однако это не означает, что качество продукции никак не контролируется.
Выбор производителя оборудования для каждой конкретной АЭС начинается с рассмотрения системы контроля качества на предприятии. Невозможно обеспечить производство качественного оборудования путем каких-то отдельных испытаний или выполнения только дополнительных требований. Качество возможно только в системе, куда включена работа с поставщиками, разработка технологических карт и контроль их точного выполнения, отслеживание рекламаций и их анализ. Только после знакомства с системой качества станция совместно с проектной организацией приступает к анализу конструкторской документации на арматуру. Несмотря на то, что документация неоднократно проверяется в рамках директивы ЕЭС о приборах, работающих под давлением, тем не менее, идет повторная проверка чертежей, расчетов и технологических карт. Только затем обсуждается план качества, выполнение которого строго документируется. Документы, входящие в план качества составляют перечень из нескольких десятков наименований и входят в комплектацию поставки. Для проведения подобных испытаний, требуется наличие испытательного оборудования и лаборатории, аккредитованной соответствующими органами, например, TÜV Австрия, привлечение независимых экспертов. Исполнение запорной арматуры для АЭС мало чем отличается от арматуры тепловых станций, отличие именно в расширенном плане качества и документальном подтверждении его соблюдения.
Основные этапы контроля:
•предварительная проверка конструкторской документации,
•проверка качества литья (корпус, штуцер, шар),
• испытания в ходе производственного процесса,
•приемочные испытания (давление/герметичность),
• маркировка и внесение в базу данных производителя, возможность отслеживания арматуры,
• подготовка итоговых документов.
Качество литья: все литьевые заготовки подвергаются капиллярной дефектоскопии и рентгенографии ( в соответствие с DIN 1690). В ходе производственного процесса особое внимание уделяется контролю сварных швов ( ведется документирование 100% сварочных работ, документирование нормализации литья, проводится дефектоскопия (капиллярная) и оптический контроль сварных швов)
Приемочные испытания включают в себя как стандартные:
•давление 1,5 от номинального. Среда: вода (DIN 3230T3-BQ = EN12266),
• герметичность наружу: 6 bar , воздух (DIN 3230T3-BF = EN12266),
так и дополнительные, по требованию станций, так, например, по требованию АЭС Гёсген в план испытаний были включены:
•тест на герметичность на проходе: 6 bar воздух (DIN 3230T3-BO класс 1),
•тест на герметичность на проходе: вода, 1,1 от номинального давления (DIN 3230T3-BN класс 1).
По требованиям других станций было увеличено контрольное время пребывания арматуры под давлением. Маркировка на корпусе содержит не только уникальный номер изделия, но и номер партии литья на каждой детали, штамп инспектора по качеству с уникальным кодом; несколько раз дублируется информация о номинальном давлении, диаметре и расчетной температуре проходящей среды. Сведения о каждом изделии сохраняются в банке данных. Выполнение таких повышенных требований контроля качества гарантирует безопасность применения арматура на трубопроводах АЭС различных классов опасности и, в конечном счете, нашу общую безопасность.